Supplying heavy-gauge, large-part pressure forming at lower quantities has insulated Ray Products from having to face much overseas competition. The simple reason, according to Jason Middleton, the company’s vice president of sales and development, is that heavy-gauge, large-part pressure forming doesn’t outsource well.
With 65 years of experience spanning three generations of family ownership, Ray Products (www.rayplastics.com) is an ISO 9001:2008 certified facility offering plastic manufacturing services that match or exceed most other processes in terms of aesthetics. The Ontario, Calif.-based company uses advanced equipment, such as fully robotic trimmers and 3D coordinate measuring systems accurate to within 1/10,000th of an inch, to produce quality parts unparalleled by overseas suppliers, according to Middleton.
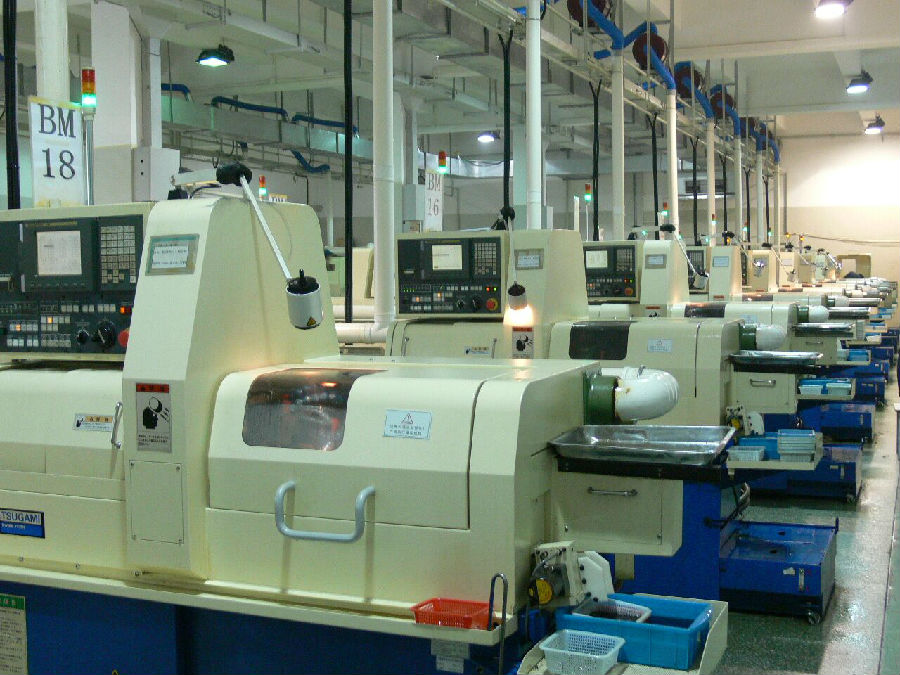
What makes pressure forming unique is that pressure-formed parts can, in many cases, match or exceed the complexity and aesthetics of injection molded parts, especially in a larger part, Middleton said in an emailed response. And when using pressure forming, the tooling costs “are a fraction of what they would be with injection molding,” he added. “As a result, pressure forming is often the most cost-effective solution for high-quality, durable plastics in quantities from the low hundreds to high thousands,” he said.
Overseas manufacturing, on the other hand, is more targeted towards making a million or more of something without any changes to design. But if an OEM is going to make 500, 2,000, or 5,000 of a part, pressure forming would be the best option, Middleton said.
“Overseas manufacturing requires high shipping costs and longer shipping times, along with frequent communication difficulties,” he said. “At higher quantities than what our process makes sense for, it might be possible to overcome those difficulties and realize some cost savings. But not at the quantities where pressure forming is the most cost-effective process.” —- by Rebecca Carnes –